SCN – The Materials Shift – choose life in the timber age
Materials shift is necessary to address the far-reaching negative health impacts that exist as a result of the extraction, manufacturing, transportation, installation, and use of building materials for our shopping centres.
Despite this, centres continue to be designed and built using low-cost, environmentally harmful materials, fueling an unhealthy materials economy to grow – while also leaving a devastating trail of destruction in its wake.
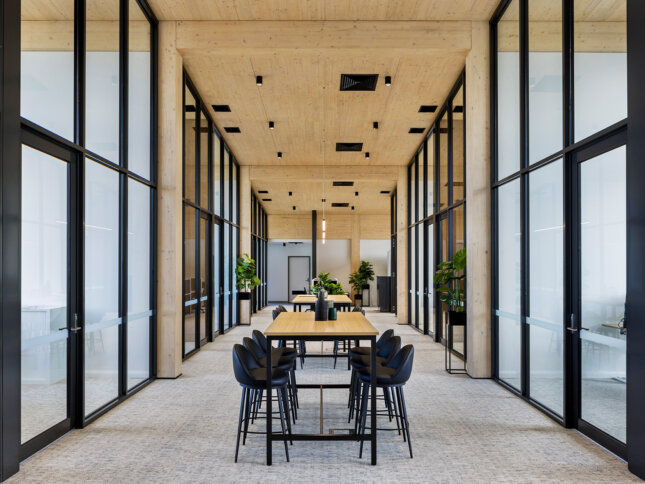
We often refer to human civilisation by the principal materials they employ, such as the Bronze Age, Iron Age etc. In this vein, the 20th century can be very much called the Concrete Age and it seems very likely that the 21st century will be the Timber Age.” – Waugh Thistleton Architects 100 Hundred Projects UK CLT (2018)
The building materials landscape is difficult to navigate due to conflicting environmental certifications. Environmental product declarations (EPD), good environmental choice accreditation (GECA), and other certifications all measure different aspects of sustainability.
There are literally hundreds of ecolabels globally. Some consider the whole life of a building product, others assess products on a pass-or-fail basis, some look at recycled content whilst others use life cycle analysis.
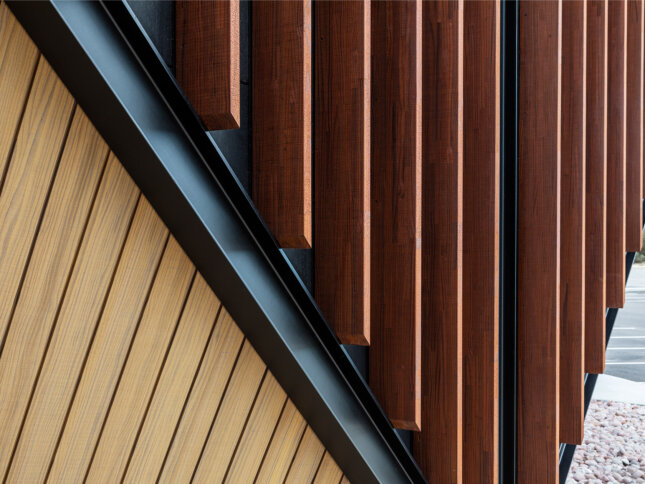
A dear friend once told me that ‘every time you purchase something you are making a choice about the way you want the world to be. If I was to translate this into our existing choices – I would concur that our future is looking pretty grim.
A materials shift is crucial to avoid chronic illness, environmental devastation, and species extinction caused by everyday products.
In order to make an informed decision about what to specify for projects, designers need transparency. Only one certification enforces full ‘Product ingredient disclosure and transparency’ and that is the ‘Declare’ certification.
Designers need to know where the product comes from, what’s in it and if it contains harmful chemicals, how it was extracted and processed and where it will go at its end of life. If a question doesn’t have an answer, then it probably needs asking. This is by no stretch a quick and easy process, but like-minded organisations are coming together as members of the Living Future Institute Australia and uniting in asking manufacturers the difficult questions.
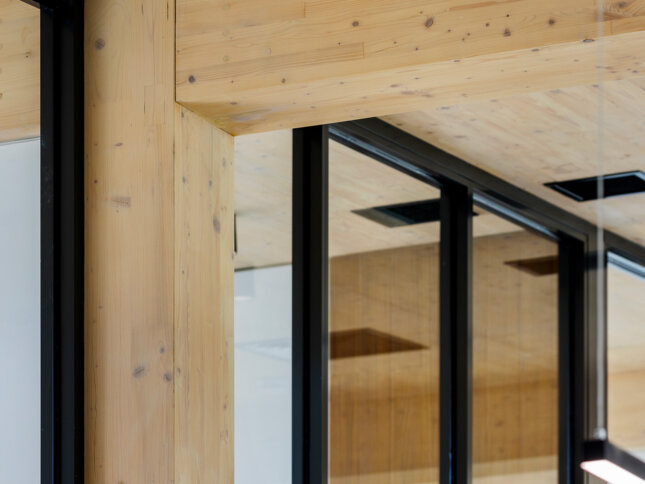
By driving a materials shift, designers can create a fair and sustainable world, one product at a time. The positive ripple effect of adopting Declare certification in the construction industry is already visible.
The International Living Future Institute (ILFI) has a comprehensive list of harmful chemicals called the ‘Red List’. It is made up of chemicals that have been found to threaten human health and wellbeing and should not be included in buildings attempting to meet the materials criteria of ILFI’s Living Building Challenge (LBC) certification process.
The Red List encompasses established chemical regulatory lists such as RoHS, REACH, Pharos, Healthy Product Declaration, Green Ideas Green Action, Building Green and Declare. The international Declare database is open and free for all to use.
The aim of the Living Building Challenge ‘materials petal’ is to promote a materials shift in the economy that is non-toxic, ecologically restorative, transparent and socially equitable. By selecting Red List compliant/ Declare certified products, designers are making a statement about the kind of future they want for their businesses, employees, families and future generations and that future is a thriving, fair, healthy world for all.
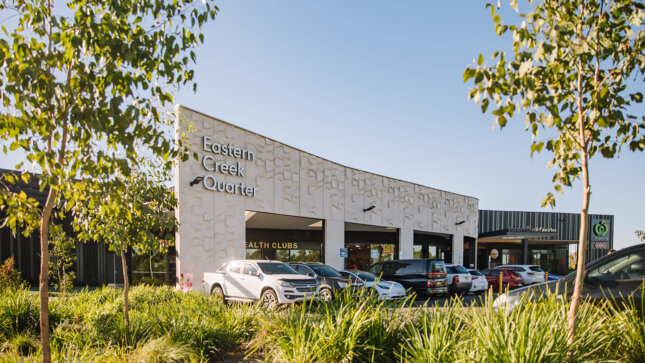
While Declare is still in its infancy here in Australia, it is growing and will have a positive ripple effect on our construction manufacturing and supplier industry.
As a rule of thumb, a deliberate move away from carbon-intensive, environmentally harmful materials such as steel and concrete would be a step in the right direction. With the recent boom in Cross Laminated Timber here in Australia, we have other viable options, so long as we know where the timber comes from and that there is an ethical supply chain.
Timber acts as a Carbon store and as a result, is a great substitute for Steel and Concrete.
“Growing trees absorb carbon dioxide from the atmosphere and store the carbon so effectively that about half the dry weight of wood is carbon. This carbon remains locked up for the life of the wood even when we use it for building products or furniture. It is only realised when the wood is burnt or rots – and wood stored in landfill under anaerobic (lack of oxygen) conditions can last for hundreds if not thousands of years.” (Naturally Better)
In addition to the carbon storage benefits, wood production requires less energy compared with other building products. According to Wood Solutions as a rule of thumb, if you convert one cubic metre of concrete for a cubic metre of timber, you will eliminate approximately one metric tonne (1000kg) of carbon dioxide from being emitted into the atmosphere.
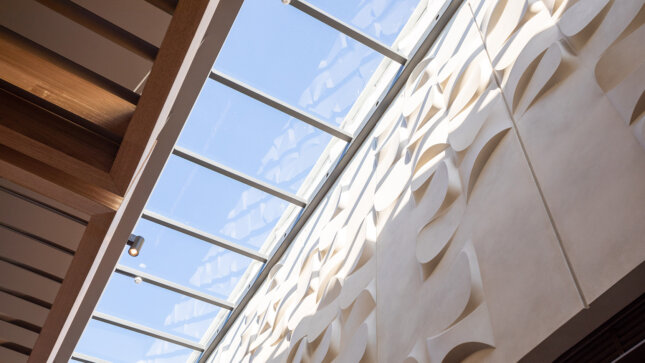
Recycled or rescued timber products should always be considered first, not only for environmental reasons but also because the weathered and repurposed timber can impart a real sense of character into the design. The irregular variation that can be created by random mixtures of species can really bring the design to life. Rescued timber can also be used to evoke interior warmth and comfort while remaining modern.
Mark & Spencer’s in Chester UK opted for timber not only for its sustainable qualities but also because it was able to express the structure and honesty of the building and reduce unnecessary finishes, which increase cost and energy maintenance demands in the future.
All timber within the store was FSC certified and some interior furniture was recycled oak from the site clearance. The external walls of the store consist of prefabricated timber-framed panels with a lime-based insulating material and a hemp and flax fibre insulating quilt, to achieve a breathable wall with a U value of 0.12W/m2K. The panels and recycled glass wool insulation within the roof help regulate the internal temperature.
This article by Associate | Regenerative Development Lead Claire Bowles was published in the July 2019 edition of SCN magazine.
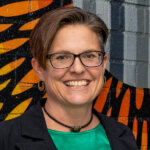
Claire Bowles
Purpose Director